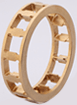
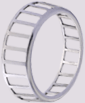
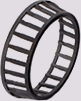
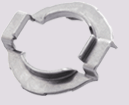
Developing skills and competency of people is a key priority area for Harsha. Reliable modules are used for internal and external training at all levels.
We have a total of 1,775 employees, of whom approximately, 1,686 employees are skilled and technically qualified employees.
HARSHA NURTURES A PROACTIVE LEARNING ECOSYSTEM TO STRENGTHEN THE TRAINING AND DEVELOPMENT ETHOS OF THE ORGANISATION.
Harsha believes in committing to the development of the Human Resource competencies, skill sets and knowledge of employees and accordingly designs HR policies which are aimed at hiring qualified individuals, developing their technical skills as well as behavioural competencies through on the job training, class room training and external training programmes. We believe that we motivate our employees for job rotation/ internal transfers for development of cross-functional/ multiple skills.
There are multiple Training rooms as well as a Technical Training Centre which imparts extended engagements through training, mock sessions and role playing.
Life at Harsha Is Stimulating, Enriching and Professionally Satisfying.
WELCOME TO HARSHA
Welcome to a world which hand holds you into a journey, which is inspiring, fulfilling, and future driven. Anchor yourself to a collaborative and creative environment, which gets the best out of you. Look up to our mentors (there are quite a few), as you will grow in the company of equals who drive organization goals through exemplary teamwork.
Ours is a dynamic workplace, be it in India or China, which itself gives you an opportunity to work with individuals with diverse backgrounds and experiences.
Engineer- Quality Assurance Apply Now
B.E Mechanical with 3- 6 years of relevant exp.to perform all activities related to QA & QC areas for particular product range.
Job Role:
Engineer- Maintenance Apply Now
B.E Mechanical with 3 - 5 years of relevant exp. Into Plan and manage the Plant Maintenance Activities, Improvement activities to achieve maintenance goals. Responsible for Machine breakdown, Plan & Manage Preventive & Corrective Maintenance. Should be Responsible for TPM activities. Maintain & Fill up the documents to fulfil TPM requirements, other documents to fulfil maintenance requirements
Competencies/ Key Skills Required:
Optimum utilization of resources to improve the machine reliability, maintainability by reducing the Maintenance cost.
Engineer- Production Apply Now
B.E Mechanical with 2- 5 years of relevant exp. into handling Production related all activities at shop floor. He must be able to handle all machine shop activities independently. Understand customer requirements and fulfill monthly production targets as per the planning. Can manage different resources Man-machine-material to achieve the production targets. Can handle Shift planning of operators. Allocation of work to operators.He must be able to work on continual improvement projects. Enhance efficiency and productivity of employees. Improve the O.E.E. of machines and enhance the productivity. Reduce defects – process variance and thereby achieve zero defect production.
Coordination with different supporting departments. (Purchase, Quality, Maintenance, Design)